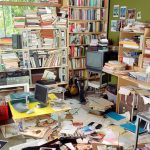
Decluttering Before Moving? 7 Professional Tips
March 21, 2024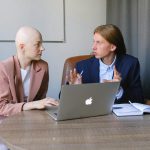
6 QUESTIONS TO ASK YOUR MOVING COMPANY
April 18, 2024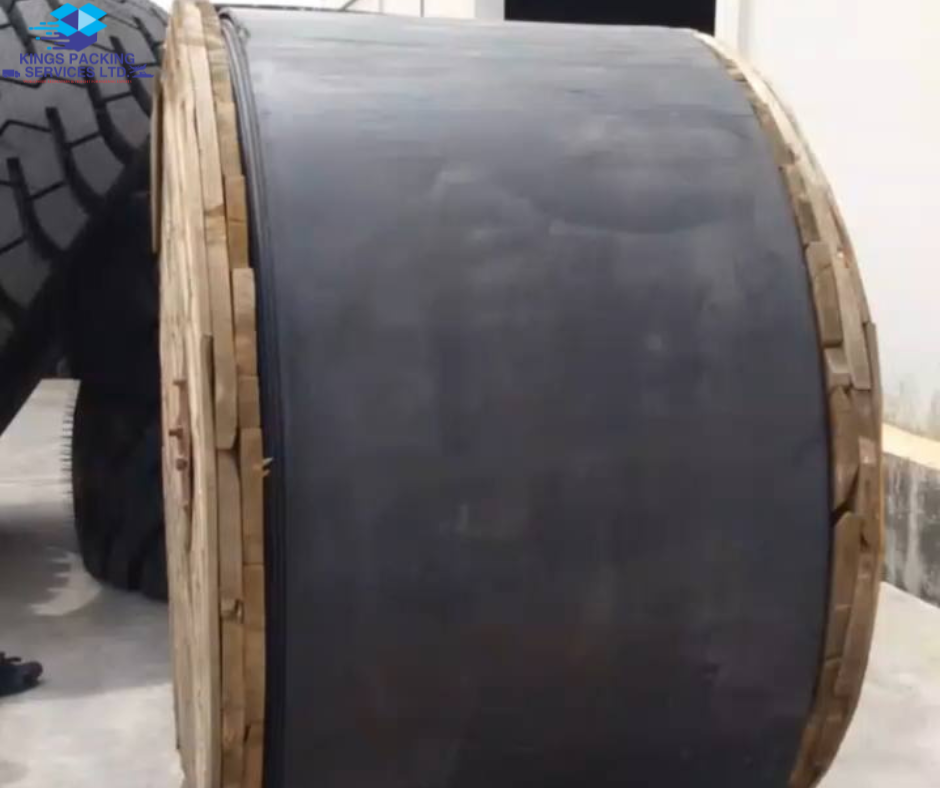
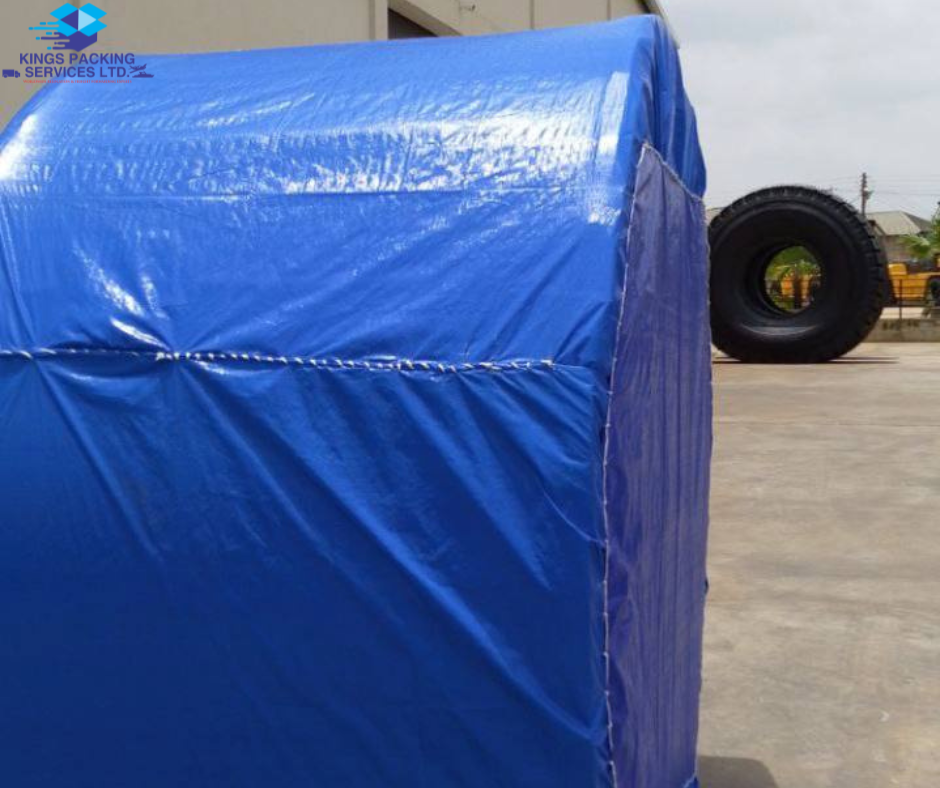
INTRODUCTION
In a recent project, the team at Kings Packing and Services Ltd (KPSL Global) was tasked with wrapping a conveyor belt for Rana Motors in Tema Community 25. While the job itself went smoothly, an unexpected challenge arose during the loading process. Despite this hiccup, the project was ultimately a success, showcasing KPSL Global's commitment to delivering quality service even in the face of adversity.
THE CHALLENGE
During the loading of the wrapped conveyor belt, a forklift inadvertently scratched the covering, causing concern for the integrity of the protection. This unexpected issue threatened to undermine the otherwise successful completion of the project.
OUR APPROACH
Despite the setback, the team at KPSL Global remained focused on finding a solution. We immediately assessed the damage and consulted with the client to determine the best course of action. Drawing on our expertise and experience, we devised a plan to repair the scratched covering and ensure the conveyor belt was adequately protected for transportation.
THE SOLUTION
Utilised specialised materials and techniques, our team meticulously repaired the scratched area of the conveyor belt covering. We conducted thorough quality checks to ensure that the integrity of the protection was fully restored. Additionally, we implemented preventive measures to minimise the risk of similar incidents in the future, including providing additional training for forklift operators on proper handling techniques.
THE OUTCOME
Thanks to our swift action and innovative solutions, the conveyor belt arrived at its destination without any further damage. Our proactive approach to problem-solving not only salvaged the project but also strengthened our relationship with the client. Despite the initial challenge, the overall success of the project reaffirmed KPSL Global's reputation for reliability and professionalism in the industry.
KEY TAKEAWAYS
1. Unexpected challenges can arise in any project, but it's how we respond to them that defines our success.
2. Effective communication and collaboration with clients are crucial in overcoming obstacles and achieving mutually beneficial outcomes.
3. Proactive measures, such as preventive training and quality checks, can help minimise the risk of future incidents and enhance overall project success.
CONCLUSION
The wrapping of the conveyor belt for Rana Motors was not without its challenges, but through determination, innovation, and a commitment to excellence, KPSL Global was able to turn adversity into triumph. This case study serves as a testament to our unwavering dedication to delivering superior service and exceeding client expectations in every project we undertake.
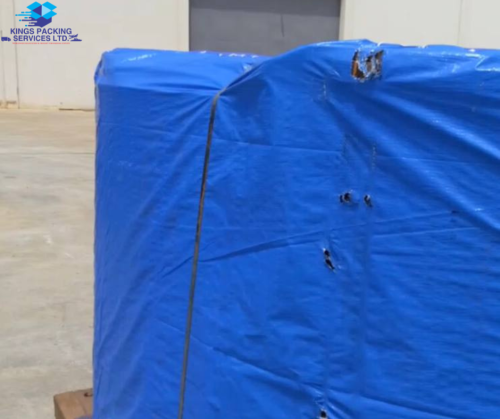
OUR APPROACH
Despite the setback, the team at KPSL Global remained focused on finding a solution. We immediately assessed the damage and consulted with the client to determine the best course of action. Drawing on our expertise and experience, we devised a plan to repair the scratched covering and ensure the conveyor belt was adequately protected for transportation.
THE SOLUTION
Utilised specialised materials and techniques, our team meticulously repaired the scratched area of the conveyor belt covering. We conducted thorough quality checks to ensure that the integrity of the protection was fully restored. Additionally, we implemented preventive measures to minimise the risk of similar incidents in the future, including providing additional training for forklift operators on proper handling techniques.
THE OUTCOME
Thanks to our swift action and innovative solutions, the conveyor belt arrived at its destination without any further damage. Our proactive approach to problem-solving not only salvaged the project but also strengthened our relationship with the client. Despite the initial challenge, the overall success of the project reaffirmed KPSL Global's reputation for reliability and professionalism in the industry.
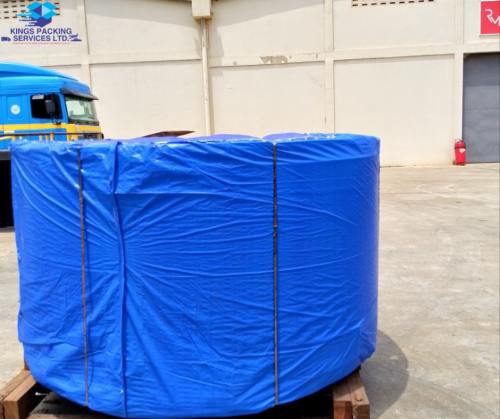
KEY TAKEAWAYS
1. Unexpected challenges can arise in any project, but it's how we respond to them that defines our success.
2. Effective communication and collaboration with clients are crucial in overcoming obstacles and achieving mutually beneficial outcomes.
3. Proactive measures, such as preventive training and quality checks, can help minimise the risk of future incidents and enhance overall project success.
CONCLUSION
The wrapping of the conveyor belt for Rana Motors was not without its challenges, but through determination, innovation, and a commitment to excellence, KPSL Global was able to turn adversity into triumph. This case study serves as a testament to our unwavering dedication to delivering superior service and exceeding client expectations in every project we undertake.